Knowledge of the chemical and mechanical properties, fabrication techniques, advantages and disadvantages of metals in general and Iron bases alloys in particular is very beneficial for structural design and analysis. Often times engineers and analysts get confused by the various terminologies used to describe the widely used Iron alloys. In this article we will attempt to provide a concise guide to Iron Alloys.
The content of this article has been derived from “Fundamentals of Materials Science and Engineering, 2000″ by William D. Callister, JR.
The figure below shows a classification scheme for the various ferrous alloys. Ferrous alloys are those in which Iron is the principal constituent.
One of the distinguishing factors for the various alloys is their percentage carbon content by weight. This can vary from 0.25% for low carbon steel up to 4.50 % in Cast Iron.
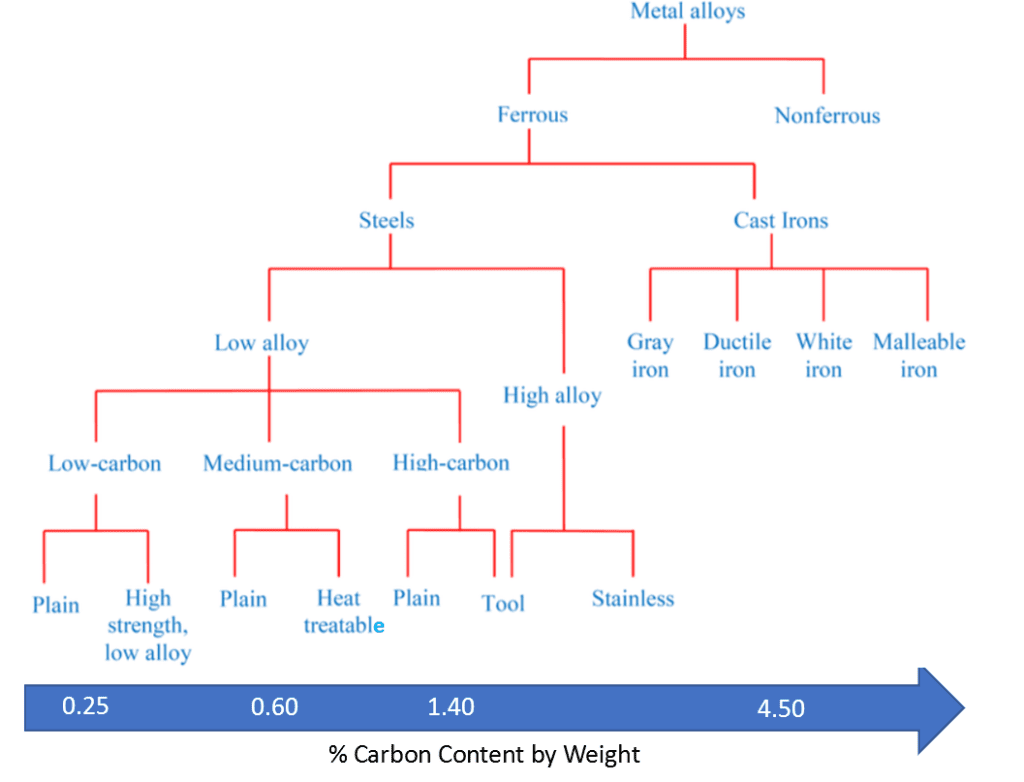
We will now list some salient features of the various alloy types in an easy to read and reference format.
Plain Low Carbon Steel
- The most common and least expensive steel
- Up to 0.25% carbon by weight
- Unresponsive to heat treatment
- Strengthened by cold working
- Relatively soft and weak
- Yield Strength ~ 275 MPa (40 ksi), Tensile Strength~ 415-550 MPa (60 – 80 ksi)
- Outstanding ductility and toughness
- Elongation of ~ 25%
- Applications: Automobile body components, structural shapes (I beams, Channels etc.)
High Strength Low Alloy Steel (HSLA)
- Include non-carbon alloying elements (Copper, Vanadium, Nickel, Molybdenum) up to 10% by weight
- Most respond to heat treatment
- Tensile Strength higher than 70 ksi
- Ductile, formable and machinable
- More resistant to corrosion than plain carbon steels
- Applications: Bridges, Towers, Support Columns, Pressure Vessels
Plain Medium Carbon Steel
- 0.25% – 0.60% Carbon by weight
- Heat treatable : Austenitizing, Quenching, Tempering
- Usually utilized in tempered condition
- Low Hardenability
Heat Treatable Medium Carbon Steel
- Addition of Chromium, Nickel and Molybdenum improves response to heat treatment
- Lower ductility and toughness than plain medium carbon steel
- Applications: Railway wheels and tracks, gears, crankshafts, machine parts and components requiring high strength, wear resistance and toughness
Plain High Carbon Steel
- 0.60% – 1.40% Carbon by weight
- Hardest and strongest among carbon steels
- Least ductile among carbon steels
- Almost always used hardened and tempered
- Wear resistant and capable of holding a sharp edge
High Carbon Tool Steel
- Chromium, Vanadium, Tungsten and Molybdenum may be added to make very hard and wear-resistant carbide compounds
- Applications: Cutting tools and dies for forming and shaping materials, knives, razors, blades, springs, high strength wire
Stainless Steel
- High alloy steels contain more than 10 % non-carbon alloying elements.
- Stainless steels contain a minimum of 11% Cr by weight
- Highly resistant to corrosion
- Corrosion resistance can be enhanced by adding Nickel and Molybdenum
Cast Iron
- Generally, 3.0 – 4.5% Carbon by weight
- Become completely liquid at 1150 – 1300 °C temperature
- Suitable for melting and casting
- Some are very brittle, so casting is the convenient fabrication technique
- Silicon is often added because it forces carbon out of solution and produces graphite
Gray Cast Iron
- Least expensive of all metallic materials
- 2.50 – 4.0 % Carbon
- 1.00 – 3.0 % Silicon
- It is gray due to the color of the fracture which is due to graphite
- Relatively weak and brittle in tension
- Much stronger and ductile in compression
- Very effective in damping vibration energy
- Suitable for machine components exposed to vibrations
- High wear resistance
- High fluidity in molten state at casting temperatures – suitable for creating intricate shapes by casting
Ductile (Nodular) Cast Iron
- Created by adding a small amount of Manganese and/or Cerium to gray iron before casting
- Graphite forms but as nodules instead of flakes
- Castings are stronger and more ductile than gray iron
- Mechanical properties are close to those of steel
White Cast Iron
- For less than 1.0% Silicon and rapid cooling rate, the carbon exists as cementite instead of graphite
- Fracture color is white
- Extremely hard, wear resistant and brittle – virtually unmachinable
- One application is rollers in rolling mills
- Often used as intermediary in the production of malleable Iron
Malleable Cast Iron
- Prolonged heating of white Iron at 800 – 900 °C alters the microstructure to produce malleable Iron
- The microstructure is similar to that of nodular iron
- Higher strength and ductility than white iron
- Applications: connecting rods, gears, flanges, pipe fittings, and valve parts for railroad and marine industry